ROLLING PROCESS
Process control
- Optimal rolling schedules
- Profile and flatness
- Interstand cooling
- Laminar cooling
Process simulation & optimization
Rolls
- Sleeved rolls
- Optimal grinding of rolls
- Optimization of BuR grinding & performance
- CoolRoll software
- Section cooling
Know-how
STRIP SUPERVISOR
Monitoring system
Specialized processor of rolling data for evaluation of strip flatness and other quality parameters
Strip Supervisor Software is specialized software designed to collect technological data of cold strip rolling, to process, to display and to store them into a unified database
- to monitor technological parameters of rolling process,
- to monitor influences of technological parameters on strip flatness,
- to eliminate the influence of human factor on the quality of the strip,
- to calculate the global quality parameters of rolled production.
For monitoring of strip flatness the Strip Supervisor requires the rolling mill being equipped with a stressometer. If the rolling mill is equipped with sectional cooling, the Strip Supervisor allows to process information about the intensity of work rolls cooling as well.
The Strip Supervisor Software collects, processes as statistically as graphically and archives the following technological information:
- strip thickness
entry and exit thickness along the length of the strip, including statistical characteristics (mean, standard deviation, percentiles, etc.), - tresses and their relation to strip waveness
longitudinal stresses in selected zones along the strip width. The maximum compressive stress and its comparison with predicted limit stress, which signals the emergence of strip waveness, - changes of the reference curve
the record of possible operator’s change the reference curve for the stressometer during the rolling process for assessing the impact of the human factor in the process of rolling, - tension forces
forward and back tension forces during the rolling process, including statistical characteristics (mean, standard deviation, percentiles, etc.), - rolling speed
entry and exit rolling speeds during the rolling process, including statistical characteristics (mean, standard deviation, percentiles, etc.), - intensity of section cooling
intensity of cooling of particular nozzles of the sectional cooling along strip width during rolling.
Particular records of technological data are supplemented by information about operators in service at the time of recording.
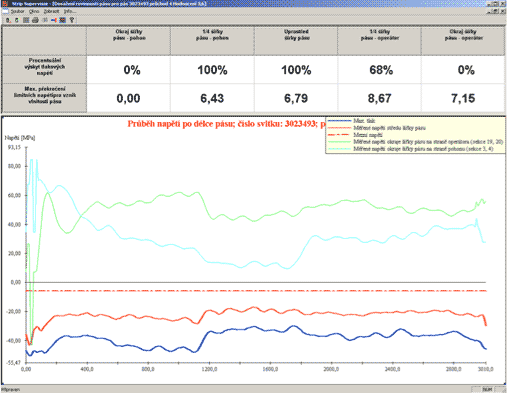
The Strip Supervisor enables comparison of different technological variables in selected locations on the strip during rolling and putting into the context their effects on the quality of the rolling process. The strip may be viewed either from above or in the selected transverse and longitudinal sections. Statistical data can be further processed in the Microsoft Office.
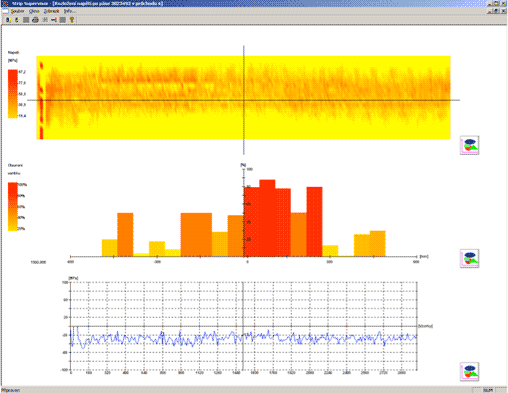
Benefits:
The main benefits resulting from implementation of the Strip Supervisor Software are following:
- allowing of a quick and conclusive monitoring of the impact of technological parameters on the strip flatness,
- allowing of a quick and conclusive monitoring of the impact of technological parameters on the strip flatness,
- eliminating of influences of human factor on the quality of strip mainly through more conclusive proving of lack of technological indiscipline of operators in service.
References:
Optimization of strip cross section in brass rolling (Měď Povrly, Povrly, Czechia)
Optimization of rolling schedules for HSM P1500 in LIBERTY Ostrava (Ostrava, Czechia)
Software module for pass schedules optimization results from the rolling technology knowledge and limiting criteria in individual phases of rolling. Limiting criteria for P1500 hot strip rolling mill (Twin Steckel) are demonstrated schematically below.
Software solution is based on mathematical optimization methods when the following two types of algorithms are applied:
- pass schedule optimization including bending forces optimization,
- pass schedule optimization and additional bending forces optimization.
On-line version of the pass schedules optimization module was implemented into Level 2 control system of P1500 rolling mill (Twin Steckel). Off-line version can be used in phase of production setup.