ROLLING PROCESS
Process control
Process simulation & optimization
Rolls
- Sleeved rolls
- Optimal grinding of rolls
- Optimization of BuR grinding & performance
- CoolRoll software
- Section cooling
Know-how
Optimization of backup rolls grinding & performance
Modul BuR Fatigue
Software module BuRFatigue for monitoring and optimization of Backup roll performance
Loads acting on backup rolls degrade their surface layer, which can lead to spalling of the surface, cracking especially in edge region of the barrel and transverse cracks of the neck. To prevent such unexpected situations the software module BuR Fatigue has been developed that enables to identify the most stressed parts of backup roll surface, calculates the accumulated damage caused by each strip (characterized by measured separating force, bending force, strip width and other parameters), predicts a suitable length of the backup roll campaign and calculates an economical dressing amount. By this way it is possible to increase the performance of backup roll and to reduce the danger of backup roll damage.
Examples of damaged backup rolls:
Grinding of backup rolls
Grinding of backup rolls removes a part of damaged layer. After grinding the residual stresses are partly redistributed but the accumulated damage of material can remain. New rolling increases the damage of the surface layer. The deeper the grinding, the more of the damaged layer have been removed and the longer new backup roll campaign can be. Too intensive grinding can lead to shortening of the BuR campaign as well.
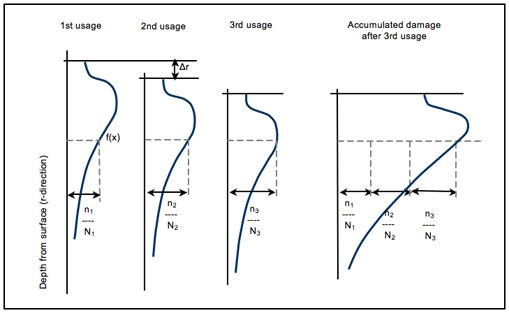
Calculation of accumulated damaged layer
The most important loading phenomena in backup rolls are as follows:
- Hertzian contact load between backup roll and work roll,
- Residual stress in roll (due to thermal treatment and other production influence),
- Bending stress.
From all stress components HMH maximum and minimum stress for each revolution of the roll is calculated. Resultant cyclic loading is transformed to symmetrical one and fatigue strength curve is constructed using Smith’s diagram and material parameters of the roll. Miner’s rule enables to evaluate various loadings and calculate accumulated fatigue damage:
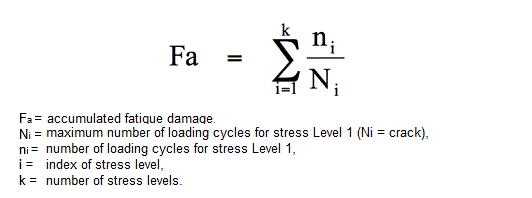
Calculated accumulated damage in surface layer after rolling of several strips can be seen in the Figure below. Maximum values can be observed in the beginning of taper on backup roll.
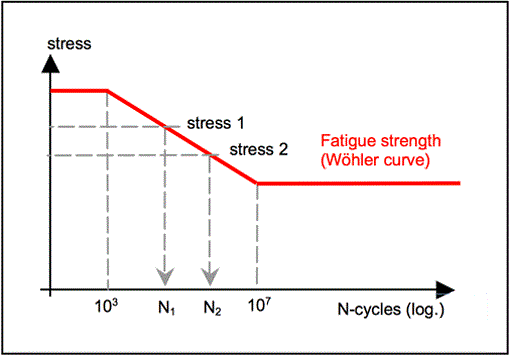
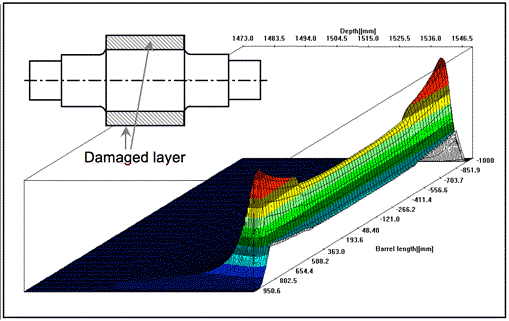
Estimation of grinding amount
Grinding amount and the length of backup roll campaign are in relation. In most mills the period of backup roll change is constant independent on its real loading. If the load of the mill is lower for various reasons (lower mill performance, unexpected shutdown etc.) grinding amount can be smaller. In opposite case of excessive performance of the mill the grinding amount should be higher or even the length of campaign should be shortened.
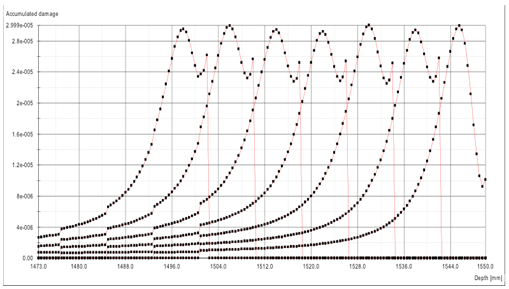
The BuR Fatique module implementation
- Monitoring of backup rolls as the submodule of the Level2
The BuRFatigue module is a part of the Level 2 and communicates directly with its Database. The software checks the level of accumulated damage and when the preset level is reached, an alarm occurs on the operator’s monitor. After finished backup roll campaign dressing amount is calculated considering the same length of the next backup roll campaign and the same loading. - Monitoring of backup rolls as the submodule of the Roll Shop Management
The BuR Fatigue module is a part of the Roll Shop Management and communicates with the Roll Shop Management Database. The Roll Shop Management collects history of loading, grinding and accumulated damage of each backup roll in the roll shop. The BuRFatigue module checks the level of accumulated damage and calculates dressing amount after finishing of each backup roll campaign. - BuR Fatigue off-line Implementation
The BuRFatigue Module is implemented into the software Rollflex and all necessary data takes from its off-line calculations.
Benefits
The main benefits resulting from implementation of the BuR Fatigue monitoring module are following:
- Optimization of the backup roll campaign
Monitoring of loading and estimation of damage accumulated in the surface layer of backup roll can prolong the roll campaign. Expensive back up rolls can be exploited longer than it was scheduled. The exploitation of each backup roll will depend on the history of its real loading so it can short its campaign sometimes and avoid unexpected total damage of the backup roll. - Controlled backup roll grinding
Estimation of the up to date depth of damaged layer enables to grind away only the necessary layer so the backup roll process life can be prolonged. The depth of the backup roll grinding becomes to be process dependent!
References:
The analysis and optimization of grinding of sleeved rolls (Springfield Machine & Tool, Inc., Battle Creek, MI, USA, 2018)
The BackUpRoll Supervisor – online monitoring of residual fatique life of backup rolls and prediction of optimum depth of dressing amount (LIBERTY Ostrava, Czech Republic)